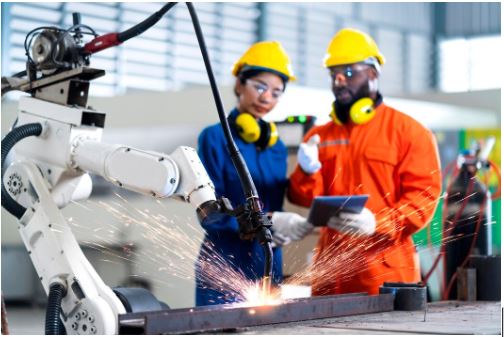
Technological advancements and trends have been the greatest contributing factor in shaping every industry. These developments have nurtured the sectors to elevate optimally while creating beneficial doors for all.
With the surfacing developments in trends and technologies, the steel industry has also progressed exponentially, catering to a broader scope of business methods and economic innovation. Plus, with the constant elevations in machinery, engineering, and techniques, the steel industry’s future has now been deemed even brighter.
As the world meets the future, in this article, learn about the cutting-edge advances of trends and technologies— shaping the steel industry’s future.
3D Printing (Additive Manufacturing) of Steel
3D Printing, also known as additive manufacturing, is an advancement in the trend and technology that has the capacity to transform the steel industry. Currently, 3D printing uses resins, powder, plastic, carbon-reinforced cement, or fibre cement. Technically speaking, this method refers to the conversion of digital computer-aided design (CAD) files into a solid three-dimensional physical object or a fragment or part of the entire object.
With 3D printing in steel production, any part of steel can be reproduced efficiently. These parts can be created faster, regardless of shape complexity and size differences. This is due to the fact that most of these parts are nearly impossible and more difficult to produce with traditional methods of manufacturing.
Moreover, this innovation can lead to massive cost-efficient savings when it comes to the waste of production materials. Plus, this method can significantly increase steel parts’ production speed and efficiency.
Furthermore, the layer-by-layer building method of 3D printing allows the production of specific materials with intricacies on steel’s high-strength and lightweight properties.
Addition of Self-Healing Materials to Steel
Researchers have recently explored the potentiality of self-healing steels. These self-healing steels will contain materials that seamlessly repair tiny cracks and insignificant damages. These advancements can remarkably extend the quality of steel parts and steel-finished structures, plunge maintenance costs, and improve the structural resilience of any building with self-healing steel.
Since steel has metal, scientists described the capacity of pure platinum pieces and copper casually healing cracks of metal steel during fatigue-inducing nanoscale experiments. They reviewed optimistically how steel with metal composites can heal a crack after stress.
Additionally, with the hope of self-healing steel, this technological ability can substantially improve the engineering industry to produce self-healing structures, equipment, and machines in the near future.
Robotic Automation in Steel Production
Automating steel production tasks has been the trend in the technology steel industry for years. Plus, with the recent developments in robotics and similar technologies already accelerating production, it is deemed to grow exponentially in the near future.
Meanwhile, robotic automation can now efficiently work on simple tasks of loading or unloading materials like raw parts and finished products. Furthermore, this production method reduces direct human labor, improves efficiency, lowers labor costs, and strategically allows the avoidance of human accidents in the workplace.
Moreover, the advent of robots that can precisely cut, efficiently weld, and accurately assemble steel enhances quality control management, improves material handling, and reduces production waste. This method allows fewer human errors, quicker project completion, and safer environments to work on.
Embracing Artificial Intelligence (AI) and Digitization in Steel Processes
Since the inception of digitization and artificial intelligence, they have always been included in discussions in every industry. Digitization and AI can bring forth sectors to intertwine more closely. Both platforms are a step forward to increased steel production productivity and efficiency.
Presently, digitization in steel production not only allows the creation of a flexible, quality, and productive working environment but also encompasses transparency of real-time data of the ongoing operation. Additionally, it provides better insights for a faster decision-making chain while reviewing the value-adding and non-value-adding processes of the production.
Meanwhile, with the incorporation of AI in the digitization of steel processes, production systems can now automatically analyze larger quantities of data supplemented by production sensors and other tools to review patterns in the process. Additionally, with this data analysis and management method, the production team can accurately predict equipment downtime, failures, and repair costs.
However, despite the rampant digital revolution, it’s important to remember that incorporating tech-based platforms doesn’t equate to eliminating human labor. Implementing well with the workforce is a step toward improved production and an effective value-adding system.
Advanced Materials to Improve the Strength of Steels
Incorporating advanced materials increases every steel’s durability, versatility, and strength in the final production cycle. These advanced materials are the following but not limited to:
- Aluminum Alloys: This alloy has a lower density compared to regular metals, allowing them to be ideal for creating lightweight structures like those seen in aerospace and cars. Additionally, this material has a high corrosion resistance and heat conductivity.
- Copper Alloys: This alloy contains an impressive conductivity to electrical and thermal sources. Plus, it’s also resistant to corrosion, making it suitable for the production of electronics.
- High-strength Iron Alloys: This composite contains more elevated levels of alloy or iron that have tensile and yield strength compared to the regular ones. This material also allows the steel to be lightweight.
- Titanium Alloys: This alloy has a notable weight-to-strength ratio and elevated resistance to corrosion. This material will allow steel to be ideal in medical equipment and aerospace projects.
- Ceramics, Fibers, and Improved Metals: These composites have specific materials with unique characteristics that can be incorporated specifically into the steel to be more applicable to low-weight and corrosive-resistance finished products.
The Takeaway
The trends and technologies discussed above have a vital role in shaping the steel industry’s future in terms of reduced cost, improved efficiency, and increased environmental sustainability. Moreover, as the world moves forward, it faces frequent natural disasters. Hence, the improved strength and durability of steel become paramount.